Enhancing Productivity and Top Quality Via Modern Metal Stamping Methods
As the needs for accuracy and effectiveness proceed to escalate, the integration of automation and electronic devices right into the metal stamping process has actually come to be extremely important. By discovering the detailed interaction between technology, automation, and precision in steel marking, a pathway towards unparalleled performance and top quality guarantee unfolds.
Benefits of Modern Steel Marking
Modern metal stamping deals many advantages in terms of performance, accuracy, and cost-effectiveness in the manufacturing industry. Among the crucial benefits of modern-day steel stamping is its capacity to successfully create high volumes of intricate steel get rid of regular quality. This procedure eliminates the requirement for multiple procedures as it can do various jobs such as blanking, puncturing, creating, and pulling in a single procedure.
Furthermore, modern steel stamping makes it possible for makers to achieve limited tolerances and exact specifications, making certain that each part fulfills the needed criteria. This high degree of precision causes minimal product waste, reduced rework, and general improved product top quality.
In addition, modern-day metal stamping is a cost-efficient manufacturing method. In essence, contemporary metal marking deals a competitive edge to makers looking to enhance efficiency and high quality in their operations.
Advanced Technologies in Metal Stamping
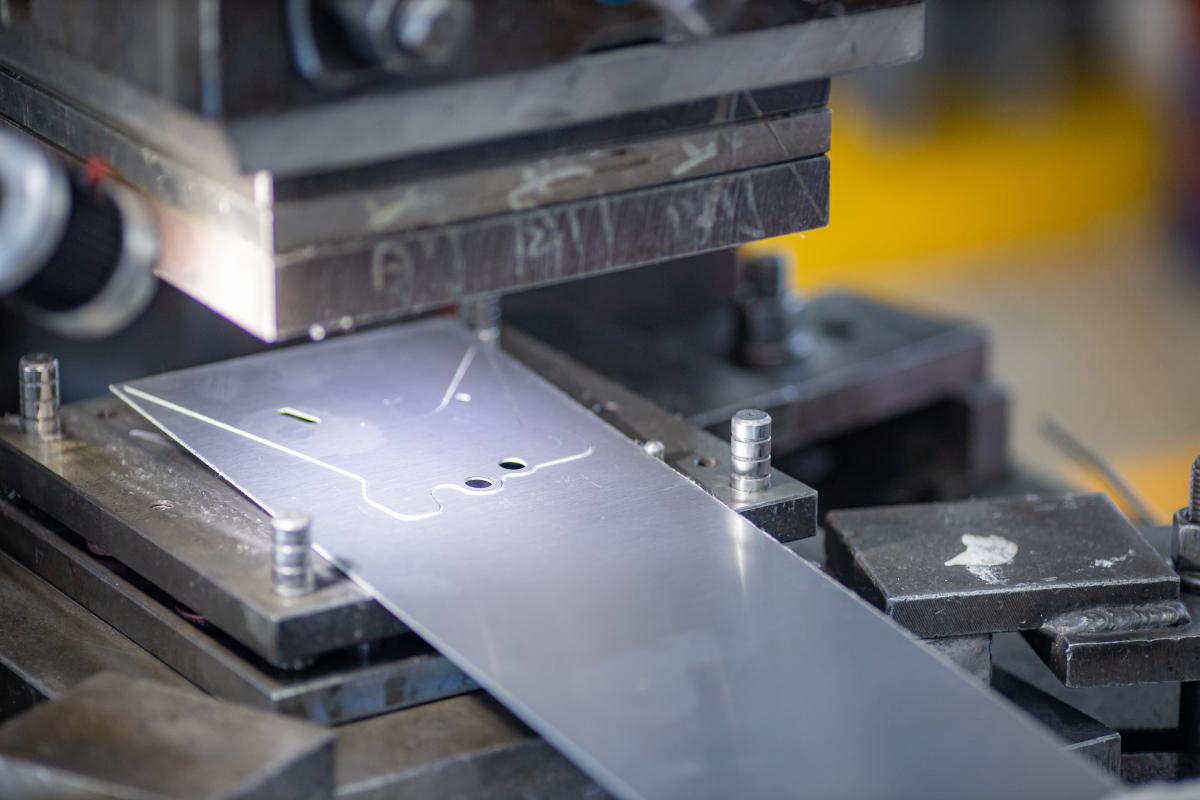
An additional crucial innovation transforming steel marking is making use of servo presses. Unlike typical mechanical presses, servo presses supply higher control over the speed and pressure applied throughout the stamping procedure. This control not only enhances the top quality of the stamped parts yet likewise reduces product waste and energy intake.
Moreover, developments in simulation software program have made it possible for suppliers to essentially evaluate and maximize the stamping procedure before physical manufacturing begins. This online prototyping helps determine potential problems early on, bring about cost financial savings and faster time-to-market for new items. Overall, these sophisticated technologies in metal marking are driving unmatched degrees of efficiency and top quality in the industry.
Improving Effectiveness Through Automation
The combination of automated systems has actually substantially enhanced the effectiveness of steel marking processes. Automation in metal marking procedures provides a myriad of advantages, consisting of increased production prices, boosted accuracy, and decreased labor prices. By utilizing robotic arms and computer-controlled machinery, jobs that were formerly time-consuming and prone to mistakes can currently my review here be implemented swiftly and with exceptional accuracy.
Automated systems have the capacity to handle repetitive jobs with uniformity, causing greater performance levels and reduced cycle times. This enhanced effectiveness not just causes set you back financial savings but also guarantees a much more structured and trusted production process. Furthermore, automation permits real-time tracking and information collection, making it possible for manufacturers to identify and deal with issues quickly, additional enhancing the general effectiveness of steel marking procedures.
Additionally, automation advertises a more secure working setting by minimizing the requirement for hands-on treatment in harmful jobs. By passing on these responsibilities to automated systems, workers can concentrate on more facility and value-added activities, adding to a more efficient and efficient process in the metal stamping sector.
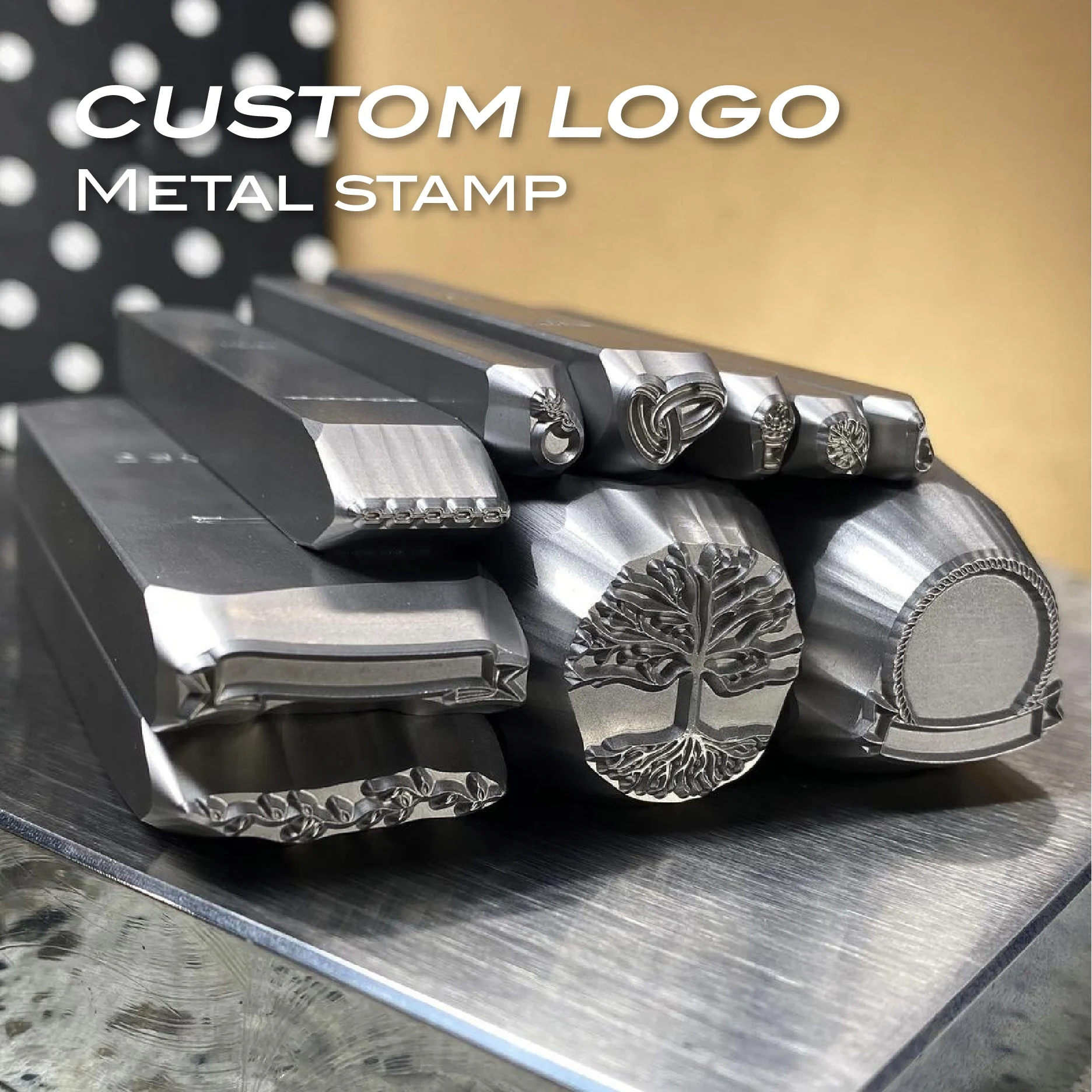
Quality Assurance Measures in Marking
Applying rigid high quality control measures is paramount in ensuring the accuracy and consistency of steel stamping procedures. By developing robust top quality control procedures, suppliers can recognize and remedy any kind of inconsistencies or flaws in the stamped parts, inevitably improving product top quality and client complete satisfaction. Among the main quality assurance procedures in metal marking is conducting normal evaluations throughout the manufacturing cycle. These evaluations entail inspecting the measurements, surface coating, and overall honesty of the stamped components to validate compliance with the given needs.
In addition, executing sophisticated modern technologies such as automated vision systems can even more enhance the top quality control process by allowing real-time surveillance and detection of any abnormalities throughout manufacturing. These systems utilize cams and computer system formulas to inspect get rid of high accuracy and precision, reducing the danger of issues escaping into the end product.
Moreover, developing a thorough documents system that records quality control data and assessment results is important for tracking performance patterns and assisting in continual improvement campaigns. By analyzing this information, manufacturers can identify possible locations for optimization and apply corrective actions to improve the total high quality of their stamped items.
Enhancing Precision With Digital Equipment
Utilizing electronic devices can dramatically improve the precision of metal marking procedures, reinventing the method makers accomplish my site precision in their production. Digital tools such as computer-aided design (CAD) software program permit the production of complex stamping designs with unbelievably exact measurements. By inputting comprehensive requirements right into the software application, producers can ensure content that each stamped item satisfies exact dimensional needs, minimizing errors and waste in the manufacturing process.
In addition, the assimilation of sensors and real-time surveillance systems in stamping equipment allows producers to closely keep an eye on the stamping procedure and make prompt modifications to guarantee precise results. These electronic tools give important information on variables such as pressure, rate, and alignment, enabling quick identification and improvement of any type of inconsistencies from the desired specs.
Conclusion
Finally, modern-day metal marking approaches offer many advantages for boosting productivity and high quality in making processes. By using sophisticated modern technologies, automation, quality control procedures, and electronic devices, companies can improve effectiveness, accuracy, and total efficiency. These innovations in metal stamping not only simplify manufacturing procedures but also guarantee constant and high-quality results. Accepting these contemporary strategies can bring about significant advancements in the manufacturing market.